Article Revised July 28th, 2022
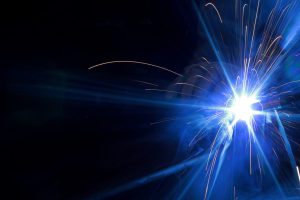
It’s often said that aluminum is a more difficult metal to weld than steel. While it’s true that most welders start out by learning to weld steel before moving on to aluminum, it’s not entirely accurate to say that one is more difficult than the other. Welding aluminum is simply different, and it requires a solid understanding of these differences in order to achieve a proper weld.
Challenges of Welding Aluminum
As we’ve discussed at length in previous blogs, aluminum and steel each have distinct characteristics, and the welding process makes some of those differences even more apparent than they might otherwise be.
One difference that stands out in particular is their thermal conductivity, or their ability to conduct heat. Because aluminum is considerably more heat conductive than steel, it has a much lower melting point. However, when aluminum is exposed to oxygen it forms a layer of aluminum oxide that has an extremely high melting point, making it not just more heat resistant, but also highly resistant to corrosion. A very clear understanding of how temperature affects aluminum is essential for skilled welders.
Another key difference involves the hydrogen’s solubility in liquid aluminum. This can lead to hydrogen bubbles forming during the liquid stage of the welding process and becoming trapped, resulting in porosity in the finished welds. If a welder isn’t accustomed to working with aluminum, porosity can become a big problem, and they may not know how to address it properly. Porosity can be mitigated by using a proper shielding gas, such as a helium/argon mixture, which protects the molten aluminum from hydrogen exposure.
A Note on the Importance of Proper Welding Filler Materials
Nowhere is it more important to use a filler selection chart than when welding aluminum. Filler charts are probably an aluminum welder’s best friend, because they take a process that could be quite complicated and codify it in a way that’s standardized. The chart takes into consideration the eight primary characteristics that most impact welding, alongside the needs of the end product that is being fabricated, to give the welder the best chance of welding success.
Interested in learning more about the differences between aluminum and steel? Check out our blogs from last month!
About EVS Metal
EVS Metal is an American precision sheet metal fabricator headquartered in Riverdale, NJ. We utilize the latest technology to cut, bend, weld, and finish stand-alone items as well as parts for integration or assembly into more complex products. Our four ISO 9001:2015-certified metal fabrication facilities comprise over 250,000 square feet of vertically integrated manufacturing space and feature the most modern equipment available, from welding robots and laser cutting solutions to automated powder coating lines.
We serve a diverse customer base across North America, providing a range of services from quick-turn prototypes to high-volume production runs. Request a personalized metal fabrication quote online, or call (973) 839-4432 to speak with a specialist today.