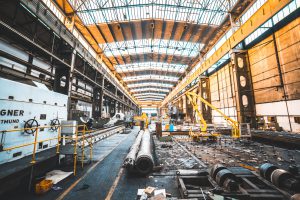
OEMs (original equipment manufacturers) can end up spending an inordinate amount of time looking for the best, most efficient processes and contract sheet metal fabricators to manufacture their products. While this is, at least on the surface, a worthy endeavor, where many go wrong is that they outsource to too many contractors. While each fabricator may indeed offer some sort of cost savings, when all factors are taken into consideration, it’s not unusual for OEMs to come out behind financially in the long run. This is due to costs that may not be readily apparent when outsourcing to multiple vendors. Today we’ll take a look at some of the most common hidden costs of inefficient outsourcing
Expenses Related to Contractor Management
The bottom line is this: the more contractors used, the more complicated it quickly becomes to coordinate and manage them. This means hiring full-time staff members dedicated to just this set of tasks. However, it’s not just their salaries that create additional costs; there are also expenses related to employee travel. Any quality-focused OEM should expect to send QA/QC staff to visit their suppliers on a semi-regular basis to ensure production is up to their company’s standards. If an OEM were to choose not to do this, then they could easily have another set of big, expensive problems on their hands if a product fails due to poor quality. This may include loss of customer confidence and ultimately, lost sales opportunities.
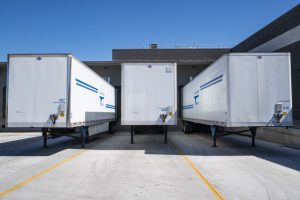
Costs of Additional Shipping and Unexpected Logistics Expenses
Just like as stated above, the more contract manufacturers used, the greater the costs in certain areas. Nowhere is that truer than in shipping and logistics. When product is being shipped from multiple locations, rather than just one or two, many of the potential cost savings are quickly eaten away due to increased freight costs. Additionally, even the most well-managed programs can run into issues including shipping and production delays and in-transit damage. When items are delivered late, it can cause problems with the scheduling of processes done onsite, such as assembly, integration and finishing. One late delivery can have a massive negative effect on the finished product’s ultimate time to market, leading to a loss in customer trust and ultimately, revenue.
Cost of Rework
There’s no way around it: the more contractors involved, the greater the chances of something going wrong. And when something goes wrong, it means a part is either going to need to be scrapped completely, or reworked. In manufacturing, there are very few errors that are inexpensive to fix. When this extra cost is added to the expense of having to manage multiple fabricators in the first place, you can be sure that most of the savings that would have been expected from outsourcing in the first place are likely null and void. In fact, it’s not uncommon for OEMs to lose money in situations like these.
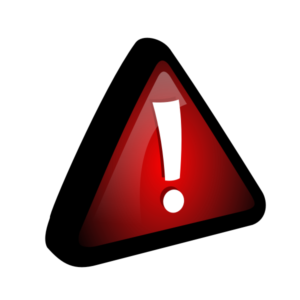
Cost of Unpredictable Risks
The more processes that are out of an OEM’s direct supervision, the greater the odds that something unpredictable could occur with one (or more) or them. This doesn’t just mean errors in fabrication. It can also mean circumstances outside of anyone’s control. These include “Acts of God,” such as hurricanes, tsunamis, earthquakes, floods, fires and other natural disasters. It can also involve man-made issues, like physical theft or theft of intellectual property. When considering outsourcing to multiple contract fabricators, it’s easy to overvalue the savings realized by cheaper labor, while completely underestimating the potential costs that may be incurred by undervaluing risk.
EVS Metal: One-Stop Contract Manufacturing and Fabrication for OEMs
The above “hidden” costs are all reasons why looking for a one-stop fabrication partner like EVS Metal can be an important strategy for reducing the expenses related to outsourcing. From design and engineering assistance, to finishing, assembly and integration, EVS is able to perform the full range of metal fabrication processes, all under one roof. This allows OEMs to realize the cost savings of outsourcing while minimizing additional expenses and risk.
EVS Metal is an American precision sheet metal fabricator headquartered in Riverdale, NJ. We utilize the latest technology to cut, bend, weld and finish stand-alone items as well as parts for integration or assembly into more complex products. Our four ISO 9001:2015-certified facilities comprise over 250,000 square feet of vertically-integrated manufacturing space and feature the most modern equipment available, from welding robots and laser cutting solutions to automated powder coating lines.
We serve a diverse customer base across North America, providing a range of services from quick-turn prototypes to high-volume production runs. Request a personalized metal fabrication quote online, or call (973) 839-4432 to speak with a specialist today.