Article Updated June 1st, 2022
Silk screening (also called serigraphy) is a common metal finishing process in metal fabrication and manufacturing. Silkscreen printing uses a fine mesh (generally made of a polyester material) and a blade or squeegee to transfer ink onto a substrate such as metal or plastic — even glass. Stencils are utilized as a part of the process to block areas of the substrate where ink should not be transferred. While silk screening can be an excellent choice to add colors or designs to metal, there are times when other methods, such as automated powder coating or direct-to-substrate printing, are better choices.
Direct-to-Substrate Printing vs. Screen Printing (Silkscreening)
Direct substrate printing (DSP) is one of the newer technologies for printing on metal, and while silk screening is still the right choice for many projects, DSP has a certain set of advantages that are important to note.
- Direct-to-substrate printing is both highly-repeatable and extremely fast. Silk screening is slower and less repeatable.
- DSP utilizes what is essentially a specialized, extra-large inkjet printer, only for metal and plastic instead of paper, making it a fully automated process with very little human intervention required (which also makes for very few man-made errors). Silk screening is usually done by hand, making it a truly custom process.
- Direct substrate printing uses CMYK colors just as a typical inkjet printer would, and is a good option for close color matching that is also cost-effective. Silkscreening, on the other hand, allows for exact color matching but requires custom-ordered ink in order to do so, which can be costly and isn’t necessary for every project.
- Unlike screen printing, DSP does not require time to air dry or “bake” to set the ink on the substrate. Instead, it uses UV curing, which is faster, and often more scratch-resistant, especially when a post-printing coating is applied.
- Direct-to-substrate printing can be completed on surfaces that are not flat, and even completely round or cylindrical, such as water bottles or golf balls. While this is possible for silkscreened items, it can be more expensive as it requires a special setup in order to do so.
Looking for precision sheet metal fabrication and machining services?
Powder Coating and Screenprint (Silkscreening) or Direct-to-Substrate Printing
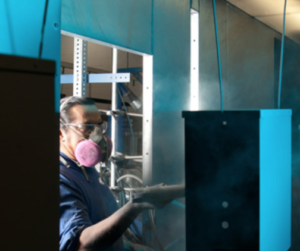
Powder coating is the application of powdered paint to a surface — usually metal but sometimes plastic — via electrostatic means. It differs from typical paint in that there is no liquid carrier, which makes it much easier to apply a thick coating of color evenly. Powder coating is a process almost always used to cover a large area, such as coating the entire surface of a stainless steel kiosk enclosure in a single color for branding purposes. Powder coating is best used in concert with screen printing or direct-to-substrate printing, as an initial process done before adding an additional design, rather than as a substitute.
Powder coating is applied via a larger “sprayer,” and is cost-effective when used for large items. Silk screening on top of the powder coat is a good choice for products that require precise PMS color matching via custom ink to achieve the desired result. By contrast, direct-to-substrate printing on powder-coated surfaces is recommended when a design needs to be created on a dimensional surface, requires high levels of repeatability, and/or must be done quickly. Powder coating is not generally considered an alternative to screen printing or direct-to-substrate printing, but instead, a complement to it, and a way to add an additional layer of color to a design.
Additional Alternatives for Printing on Metal
There are other alternatives for printing on metal, including gravure and flexographic printing. Both of these metal finishing types belong in the conventional printing category, which means they all require a print master or a print form (a big advantage of direct-to-substrate printing is that a print master is not required). Gravure printing results in extremely sharp resolution at fast printing speeds, but it is not recommended for most jobs due to its extremely high cost. Flexo also results in excellent print resolution but is generally too slow for most fabricators’ needs. While both can be used on metal, they would rarely be the first or even second choice for most metal fabricators, which is why EVS has invested in DSP and silk screening rather than flexo or gravure.
Why choose EVS Metal for powder coating, direct-to-substrate printing, and silkscreening?
EVS Metal is an end-to-end fabricator and manufacturer with locations in four states — all of which feature fully-automated in-house powder coating lines (New Jersey, New Hampshire, Pennsylvania, and Texas, with a fourth opening in Pennsylvania in 2021). Our New Jersey metal fabrication facility also offers direct-to-substrate printing and silk screening for more complex finishing needs. For more information about our metal finishing processes or to get a quote for a metal finishing project, contact us via our website, or call 1-888-9EVS-MET to speak to a specialist.