Article Revised August 22nd, 2022
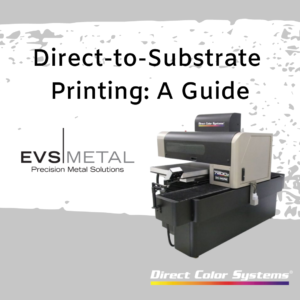
Direct-to-substrate printing (DTSP) utilizes inkjet technology to print high-quality, full-color images directly onto a variety of substrates, including metals such as stainless steel and aluminum, as well as other materials like wood, plastics, glass, ceramics, PVC, and acrylics.
Direct-to-substrate printers are not only able to print on flat surfaces but also on objects of various dimensions, including those that are conical, cylindrical, or spherical. For instance, you can even customize aluminum water bottles and golf balls via DTSP.
Direct-to-Substrate Printing: How Does it Work?
Direct-to-substrate printing utilizes the same basic principles as inkjet printing but with the addition of a few very specific technologies. The first is the size of the flatbed onto which an object is placed for printing — It’s much bigger than any typical inkjet printer. For example, EVS Metal’s new DCS 7200z has a printable area of up to 23.8”3 x 48.0”.
Direct-to-substrate printers are also unique in that they apply a special type of ink that contains acrylic monomers, which allow the ink to bond directly to the substrate via UV curing. That curing triggers a polymerization process that directly adheres the printed image/ink to the substrate.
Direct-to-Substrate Printing: Features and Benefits in Metal Fabrication Applications
As mentioned previously, DTS printers make it possible to print clear images on various substrates of many different sizes. However, there are other benefits as well, including:
- Repeatability/consistency of printing
- Speed of printing; up to 320 ft2/hr
- Does not require the substrate surface to be primed prior to printing
- Ultra-high-resolution printed images of up to 5760 dpi
- A full range of ink colors and combinations are available and can be printed via the use of PMS numbers
- Printed substrate does not need time to “dry;” UV curing immediately polymerizes and bonds the ink to the substrate surface
- True white ink options are available, allowing printing to take place even on very dark substrates
- Clear overcoat ink can be applied to printed images for greater scratch resistance and durability for fabricated metal products
Why Choose Direct-to-Substrate Printing to Finish Fabricated Metal Parts?
Historically, metal fabricators have primarily used silk-screening processes for many projects that can now be completed more quickly, easily, and consistently via direct-to-substrate printing. And screen printing still does the job of “printing” on metal for many projects quite well. However, it is not an ideal finishing process for certain fabricated metal finishing jobs, especially those that must be both highly repeatable and completed fast. This is because screen printing requires post-ink application heat curing to adhere the ink to the metal as a secondary process, adding to overall lead times. Additionally, exact color matching is nearly impossible, as the process isn’t computerized, unlike with DTS printing, which utilizes PMS colors for precisely-controlled results.
Essentially, when precision, speed, repeatability, and consistency are paramount, direct-to-substrate printing is often a better choice than silk screening. It leads to decreased production and handling time and offers greater flexibility due to its advanced digital functionality. For EVS Metal, this means we are able to meet or exceed our customers’ expectations on time, every time, with the quality, service, and attention to detail they’ve come to expect from EVS.
Interested in EVS Metal’s Direct-to-Substrate Printing Capabilities for Your Fabricated Metal Project?
Request a personalized metal fabrication quote online or call 1-888-9EVSMET to speak with a specialist today.
About EVS Metal
EVS Metal is an American precision metal fabricator headquartered in Riverdale, NJ. We serve a diverse customer base across North America, providing a range of services from quick-turn prototypes to high-volume production runs. Our machinists and operators utilize the latest technology to cut, bend and finish stand-alone items as well as parts for integration or assembly into more complex products.
Our four ISO 9001:2015-certified locations in NJ, TX, PA and NH comprise over 250,000 square feet of vertically-integrated manufacturing space and feature the most modern equipment available, from lasers and CNC machining centers to automated powder coating lines.