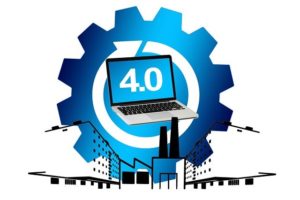
Many may have heard of Industry 4.0, but it wasn’t until recently that the “fourth industrial revolution” began to take hold in any practical sense. Now that it is starting to gain traction, questions are starting to arise about what it means for manufacturing and metal fabrication in terms of real-world implications.
What is Industry 4.0?
First off, Industry 4.0 is simply a way of describing the current trend of automation as it applies to manufacturing. It involves some of the most talked-about aspects of automation technology, including cloud computing, the Internet of Things (IoT) and cyber-physical systems.
How do automation, “the cloud,” and IoT work together as part of Industry 4.0?
In order to understand how these pieces interact with one another to create an Industry 4.0 environment, it’s best to include a quick overview of what these technologies are and do:
- IoT: The idea that any device that can be turned on or off can be connected to the internet, or another IoT device. This isn’t limited to just home appliances, and can also apply to machine components, even those integrated into industrial manufacturing equipment.
- Cloud Computing: A model for enabling on-demand network access to a shared pool of computing resources such as networks, servers or storage that can be accessed and utilized with minimal management.
- Cyber-physical systems (CPS) are built upon the idea of seamless integration of computational algorithms and physical components. It’s utilization results in greater adaptability, scalability, resiliency, safety and usability than current “embedded” system types.
When taken together, the above form the foundation of Industry 4.0 and everything it touches, including manufacturing. In EVS Metal’s case, it will eventually impact the way we fabricate and machine both single items and finished products, from start to finish, including warehousing and shipping, whether we’re manufacturing full production runs, or single prototypes. Simply put, this “fourth industrial revolution” is the advent of the first truly “smart factory,” one in which decisions are able to be decentralized and streamlined, errors and waste are kept to an absolute minimum, while time, physical space, and materials usage are optimized for the best possible outcomes.
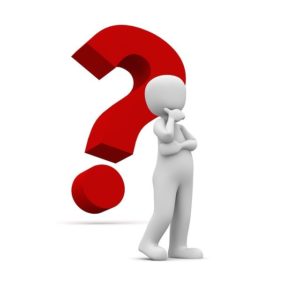
How is Industry 4.0 viewed by influencers and thought leaders?
International consulting firm McKinsey and Company believes that it is more than just a flashy catchphrase, and is instead “A confluence of trends and technologies that promises to reshape the way things are made.” They released an in-depth analysis covering a range of Industry 4.0 topics, including those relevant to the manufacturing sector, such as the use of advanced robotics and 3D printing. While it was noted in the report that not all of the technologies examined may be scalable at the moment, advances are being made so rapidly that costs are expected to drop in the near future to the point where broad industrial applications will not just be possible, but probable, including those meant for manufacturing and fabrication environments.
Because of its focus on smart technology, including some forms of artificial intelligence, it might initially be easy to be scared off or intimidated by the idea of Industry 4.0. After all, we’ve been told for decades that the “rise of the machines” is imminent. To some extent this is true, but what needs to be considered is that, like most technologically advanced systems, these cyber-enabled “smart machines” are most effective when utilized in concert with human support. People and machines simply do not “think” or process in the same ways. Additionally, many of the tasks automated via Industry 4.0 technology are generally considered undesirable by most people, be they too repetitive, too tiring or just plainly unsafe. With the market for smart machines expected to increase at rate of 15% over the next four years, it’s clear that there is pent-up demand for new technologies that will only continue to expand as they become more reliable and affordable.
Industry 4.0 and Smart Machines
Smart machines are one aspect of the smart factory, and potentially the most important. While it may sound convoluted, it’s not nearly as complicated to understand what a smart machine is as it might at first seem.
Any device that is considered “intelligent” is a smart machine. For instance:
- Generally, smart machines must use machine-to-machine (M2M) technology
- Smart machines are able to solve problems/make decisions without constant human guidance.
- Smart machines often have the capability to seemingly “learn” via complex algorithms, which over time, can make them more efficient and less prone to error.
To a certain and somewhat unfortunate extent, we’ve been taught to fear machine learning, but rest assured, this is not the same thing as a computer gaining a sort of human consciousness. Nor does it signal that the end is near for skilled labor positions in manufacturing. While employees will need to be willing to evolve and adapt as part of their re-education, primarily in branches of mechatronics, smart factories will represent more than anything a change rather than an elimination of skilled manufacturing jobs.
Another impact of smart machines and smart factories on the labor force is the possibility it holds to actually bring manufacturing jobs back to the United States in a process known as “onshoring.” Although the initial cost to invest in Industry 4.0 technology can seem exceedingly high, once installed and running, smart automation can eliminate many of the labor costs that caused offshoring in the first place. Smart machines allow for faster, more efficient production, so while they may replace certain kinds of inexpensive unskilled labor, there will still be plenty of jobs available to those willing to retrain for more technologically skilled positions working with these advanced systems. Only now, the jobs will be here in the U.S., rather than outsourced to China, India or Mexico.
Smart Machinines in Manufacturing Environments
Today’s CNC machining systems — such as our Amada Laser Cutting System with Rotary Index (FOM2 3015 NT RI) — are pretty amazing. In fact, it is one of the most technologically-advanced machines we operate at EVS Metal and includes a substantial amount of automated functionality. But what if it was not just advanced, but truly “smart?” As fabrication evolves, so will the systems around it, allowing for greater flexibility, adaptability and scalability. This may not even mean the need to replace machines, so much as it may mean their retrofitting. The addition of something as relatively inexpensive as smart sensors to monitor excessive heat output and parts wear or to report other useful diagnostic information would go a long way toward decreasing downtime and extending machines’ useful lives (and therefore preventing fabricators from spending hundreds of thousands of dollars in new equipment that may be better spent elsewhere).
In a fascinating development, Seiko Epson, a Japanese technology company, has created an autonomous dual-arm smart robot that they believe creates opportunities for greater flexibility and productivity in high-mix, low-volume manufacturing environments like EVS Metal. With its moving head, arms that are capable of grasping objects and cameras that function as “eyes” in both its head and hands, “this robot has the ability to recognize 3D objects and make visual inspections,” says Minoru Usui, the company’s president. When combined with advanced 3D printing technologies, IoT and cloud computing, it’s clear that these types of smart machine advances may soon make “just in time” manufacturing the standard across the industry.
The Global Movement Toward Industry 4.0
- Japan and Germany are the farthest along in digitizing internal operations and partnering across their value chains.
- The German government is investing approximately $216 million to encourage research around Industry (Industrie) 4.0, including funding for universities and private organizations.
- The United States doesn’t plan on being left behind in the Industry 4.0 race; it is home to the not-for-profit Smart Manufacturing Leadership Consortium (SMLC), whose goal is to create an open smart manufacturing platform for the industrial IoT so companies of all sizes have affordable access to these technologies.
- Cisco stated that it believes startups may have a unique opportunity to benefit from Industry 4.0 as they will be able to implement related processes from the start, rather than suffering through a long period of retrofitting likely to be experienced by more entrenched manufacturers, giving them a better shot at a slice of the $148 million UK pie.
- Global investments at this time suggest that companies will invest $907 billion per year through 2020.
Bottom-Line Impact of the Fourth Industrial Revolution
- Accenture reported in early 2015 that Industry 4.0 could add as much as $14.2 trillion to the world economy over the next decade and a half.
- 35% of manufacturers expect revenue gains of more than 20% over the next five years.
- 86% foresee simultaneous gains from both lower costs and added revenue in the next five years.
PriceWaterhouseCoopers’ Landmark Survey
In 2016, PwC conducted the most comprehensive Industry 4.0 survey to date, encompassing 2000 participants across nine industry sectors. They found that Industry 4.0 as it currently stands is primarily focused on the end-to-end digitization of physical assets and their integration into digital ecosystems with value chain partners encompassing a broad spectrum of technologies. Some of the paper’s highlights include the following:
- Three key attributes of Industry 4.0 include digitization and integration of vertical and horizontal value chains; digitization of product and service offerings; and digital business models and customer access.
- Those surveyed expected to realize annual revenue increases of almost 3% through 2020, while reducing costs by 3.6% and increasing efficiency by 4.1%.
- Investing in greater digitization and support for enterprise-wide integration is predicted to increase 118% by 2020 in support of Industry 4.0.
- 33% of manufacturers surveyed report they have a high level of digitization today, projected to increase to 72% by 2020.
- 83% expect data to have a significant impact on their decision-making in five years; only about half are currently using data to drive decisions.
- Globally, manufacturing enterprises expect to gain an additional 2.9% in digital revenues per year through 2020.
- New product development and optimizing existing products and services are the greatest areas of growth potential for analytics in manufacturing by 2020
- Investing in greater digitization and support for enterprise-wide integration is predicted to increase 118% by 2020 in support of Industry 4.0.
Overall, PwC found that generating, analyzing and communicating data seamlessly is what underpins the gains promised by Industry 4.0. It’s this networking of data that will eventually harness the wide range of new technologies becoming available, ultimately creating value.
So what’s next for Industry 4.0? While it’s impossible to predict the future, what we do know is that it’s here to stay and EVS Metal is ready to take on its challenges in order to reap all of its various benefits both for us, and for our customers, in the coming years.