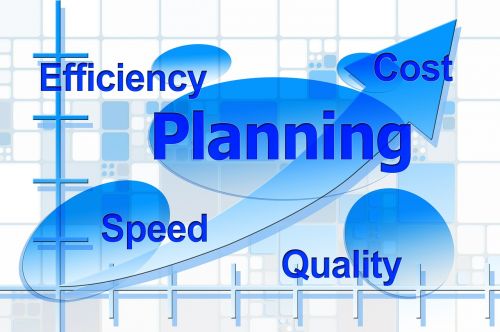
Last week, we began a discussion on utilizing lean principles in traditional job shops. We continue this week by taking a look at exactly how high-mix, low-volume environments can incorporate and benefit from these ideas, even when the focus must be on production, rather than product.
How can lean practices be implemented in high-mix, low-volume fabrication shops?
Moving toward a lean job shop floor in a high-mix, low-volume environment may ultimately require a different perspective, but the foundational principles of lean must still be followed, at least at the start. Assessing all types of waste is still necessary, and can include any number of areas, such as excessive inventory, overproduction and underutilization of both people and resources.
The waste assessment should also include a careful evaluation of information waste — something not covered under traditional lean guidelines. Information waste is the product of too much information being conveyed without the precision, accuracy and conciseness required to make the system run smoothly. It comes down to training employees on the shop floor to be efficient, fluent communicators so that projects are completed correctly the first time, eliminating mistakes and the resulting rework.
How has EVS Metal implemented lean manufacturing practices?
One way EVS Metal eliminates information waste is via what’s actually a very traditional lean system — 5S — which stands for sort, straighten, shine, standardize and sustain. 5S helps create an organized workplace by clearly identifying and storing necessary tools, visually outlining processes and maintaining work areas over time. This allows for the standardization of workflow and ultimately encourages efficient, accurate and consistent communication between employees and departments.
Another tool EVS uses may seem obvious, but is often surprisingly underutilized by many companies — measurement. By creating a baseline of operations, we are able to measure not just our progress as a lean manufacturer, but we’re able to empower our managers to identify additional ways to improve the shop floor. This can include changing processes, identifying employees who may benefit from additional training and reviewing data variables over time in order to identify which types of jobs are most valuable to the company in terms of revenue.
As a high-mix, low-volume lean metal fabrication and manufacturing shop, we use the above tools and systems to systemically streamline our work processes, ultimately leading to greater efficiency, decreased costs and faster production times. This creates value for our customers in several ways, including quick prototype completion, allowing for faster, more nimble turnaround on future iterations, ultimately allowing for an accelerated movement of new products to market.
Ready to discover how EVS’s use of lean systems can benefit your company? Simply request a quote online, or call us at (973) 839-4432 today.