Article Revised August 19th, 2022
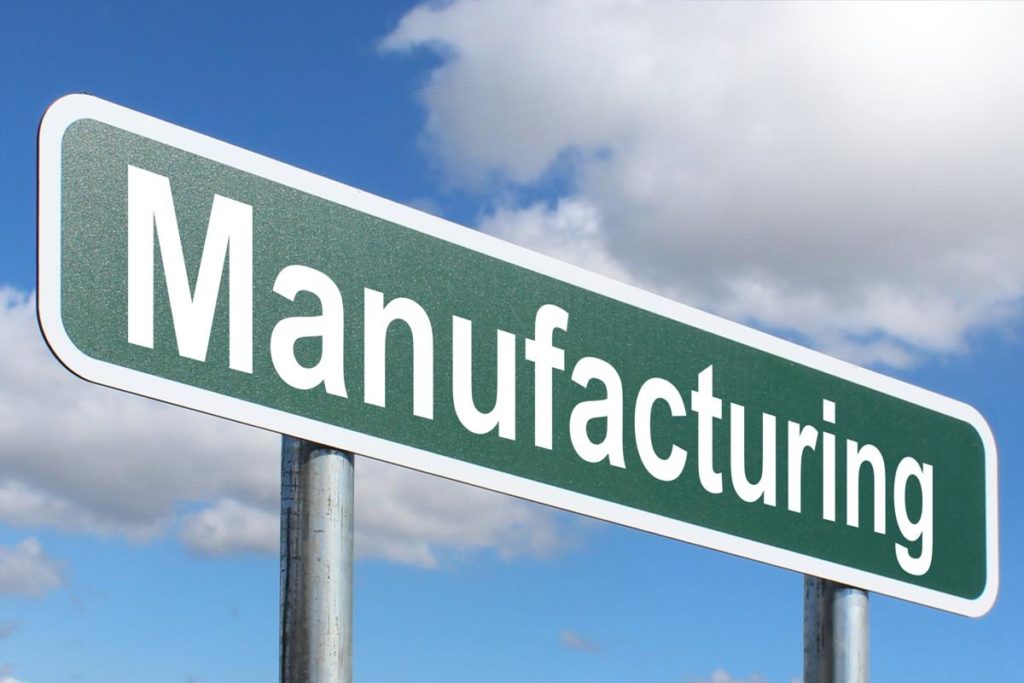
The origins of lean manufacturing can be found in the Toyota Production System (TPS) philosophy of the 1980s. This management style centers around the idea that reducing processes and positions down to the bare necessities makes it much easier to see what’s important or adds the most value.
What are the positive effects of implementing lean manufacturing?
At its most basic, lean manufacturing focuses on the elimination of waste; not just physical waste, as in an excess of materials, but also waste that occurs as the result of overburdening, or via uneven workloads. It systemically streamlines the entire manufacturing system to make it as efficient as possible, ultimately leading to greater efficiency, lower costs and faster production times. In fact, research has shown that when lean principles are put into place, it can produce significant results, including reduced manufacturing lead times and floor space requirements, and increased first-pass yields, throughput and productivity.
When did other types of manufacturers begin implementing lean practices?
Lean manufacturing was originally developed based on the high-volume, low-mix needs of the auto industry. This type of mix allows for a kind of balanced workflow that just isn’t possible in most low- or low-to-mid-volume, high-mix shops, making it an intimidating and seemingly impossible system to incorporate into the shop floors of typical American manufacturing companies. However, around 20 years ago, this brand of manufacturing slowly began to find ways to successfully adapt the lean philosophy for their own circumstances — including EVS Metal.
How have low-volume, high-mix shops like EVS made lean manufacturing work for them? By turning classical lean on its head and focusing on process over product — the exact opposite of the traditional TPS philosophy that inspired lean in the first place. Utilizing lean in this manner doesn’t mean that the original tenets are ignored; it simply means that the emphasis is instead on reducing waste in terms of issues like machine uptime and fast response.
How does EVS Metal use lean processes in their precision sheet metal fabrication facilities?
As a lean metal fabrication and manufacturing shop, we use the tools and systems that form the framework of the lean philosophy to systemically streamline our work processes, ultimately leading to greater efficiency, decreased costs and faster production times. This creates value for our customers in several ways, including quick prototype completion, allowing for faster, more nimble turnaround on future iterations, which ultimately allows for an accelerated movement of new products to market.
Next week, we’ll talk more about incorporating lean practices in traditional job shop environments. However, if you’re ready to discover how EVS’s use of lean systems can benefit your company, simply request a quote online, or call us at (973) 839-4432 today.
When did other types of manufacturers begin implementing lean practices?
Lean manufacturing was originally developed based on the high-volume, low-mix needs of the auto industry. This type of mix allows for a kind of balanced workflow that just isn’t possible in most low- or low-to-mid-volume, high-mix shops, making it an intimidating and seemingly impossible system to incorporate into the shop floors of typical American manufacturing companies. However, around 20 years ago, this brand of manufacturing slowly began to find ways to successfully adapt the lean philosophy for their own circumstances — including EVS Metal.
How have low-volume, high-mix shops like EVS made lean manufacturing work for them? By turning classical lean on its head and focusing on process over product — the exact opposite of the traditional TPS philosophy that inspired lean in the first place. Utilizing lean in this manner doesn’t mean that the original tenets are ignored; it simply means that the emphasis is instead on reducing waste in terms of issues like machine uptime and fast response.
Looking for precision sheet metal fabrication and machining services?
How does EVS Metal use lean processes in their precision sheet metal fabrication facilities?
As a lean metal fabrication and manufacturing shop, we use the tools and systems that form the framework of the lean philosophy to systemically streamline our work processes, ultimately leading to greater efficiency, decreased costs and faster production times. This creates value for our customers in several ways, including quick prototype completion, allowing for faster, more nimble turnaround on future iterations, which ultimately allows for an accelerated movement of new products to market.
Next week, we’ll talk more about incorporating lean practices in traditional job shop environments. However, if you’re ready to discover how EVS’s use of lean systems can benefit your company, simply request a quote online, or call us at (973) 839-4432 today.