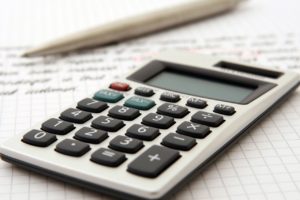
In terms of the supply chain, businesses need to be concerned with many different factors. Speed, efficiency, quality of services provided and costs involved are just a few of the considerations that require scrutiny when deciding how to manage and deploy the many moving parts of a typical supply chain. Of the different issues, it’s impossible to say which is most important; they all play significant roles in the success of a business. However, each factor will still ultimately be more affected by one aspect than any other: the controlling of costs. Because there are so many variables that can come into play and influence costs, businesses often fail to recognize that one of the biggest contributors to projects going over budget can be seen well in advance, and that’s Total Landed Cost (TLC).
What costs are included in a total landed cost calculation?
Total landed cost refers to the total of all costs associated with delivering a product, from start to finish. This includes everything from initial product concepting and design, to fabrication and finishing, to logistics and marketing. Basically, every single element that comes into play from the beginning of a project through the time revenue is actually produced. The problem is that while a typical supply chain manager recognizes the obvious contributors to cost, such as the ones listed previously, he may entirely miss some of those that can be less so, especially when dealing with overseas vendors, such as:
- Carrying costs
- Corporate income tax
- Carbon footprint
- Currency exchange rates for several different countries
- Multiple country-specific tariffs and taxes
- Risk management
Why an Accurate Total Landed Cost Calculation is Important
The key is to make supply chain decisions based on a truly comprehensive data set. The problem, though, is that getting that type of data can be difficult, making it even harder to make an accurate TLC calculation. As a manufacturer in an industry that can be more than a little chaotic, it can be easy to think that letting small things slide when business is rolling in isn’t going to make a big difference in the end; after all, products often take months if not years to bring to market; it can be a long road. But the truth is that even tiny overruns on budget often snowball into bigger ones down the line. Having a complete understanding of how much a product costs to produce and sell throughout its entire lifecycle can mean the difference between profit and loss.
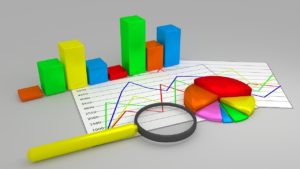
The True Cost of Outsourcing Metal Fabrication & Manufacturing to Overseas Companies
We discussed previously how not giving adequate attention to TLC in order to calculate the true price of a product when considering potential suppliers is one of the easiest ways for businesses to end up with expenditures that are out of line with what they had expected to invest. One way to fall into this trap is assuming that, when comparing domestic vs overseas vendor costs, the overseas vendor estimates are definitely cheaper, just because their net purchasing costs appear lower. Unfortunately, there’s an excellent chance that there are many “hidden costs” that are not being factored into the estimate that are associated with using a foreign vendor. These can include transportation costs, customs, tariffs and taxes that would not come into play when using a domestic supplier, instead.
Onshoring Manufacturing Services: Quality and Cost Control
In fact, while manufacturing companies have pursued opportunities to offshore labor and production over the last decade, research has shown that the savings garnered by going this route were often negligible or even non-existent. It turns out that the additional costs associated with overseas sourcing almost completely offset the potential savings from cheaper labor. Hard evidence of this was illustrated by MIT design for manufacture expert David Meeker. Meeker, along with procurement and finance expert Jay P. Mortensen, reported that manufacturers repeatedly miss the hidden costs when outsourcing to countries with lower labor costs. The two went on to say that simply applying design for manufacture (DFM) principles (of which accurate calculation of TLC is one) during the course of doing business would allow companies to realize the savings they had hoped to get from foreign labor, while still allowing them to use domestic suppliers.
Additionally, domestic vendors hold the considerable advantage of simplified communication (the same or similar time zone vs a 12-14 hour time difference), meaning fewer man-hours are required to ensure a project is kept moving along at the expected rate. This results in shorter lead times and quicker time to market, ultimately enabling the company to turn a profit faster.
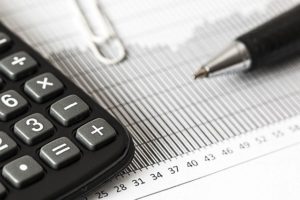
How Innacurate TLC Calculations Can Hurt
When companies fail to calculate the true TLC of a product, it puts them at a severe disadvantage in a highly competitive, global marketplace. The problem is that it can be difficult and complicated to get a full picture of TLC — not to mention, time-consuming. But it’s the only way to completely understand expenditures at each point in the supply chain, and therefore, find ways to improve.
It’s important to know that there isn’t only one way to calculate Total Landed Cost — it will look slightly different for each industry and company. However, the broader the formula, the less effective the calculation will be; taking the time to gather as much information as possible is the entire point of the exercise. Companies use a range of tools to understand their TLC — larger businesses often invest in sophisticated software, but for smaller organizations, an in-house created spreadsheet can often be just as effective, as well as less expensive.
What Should be Included in Total Landed Cost Calculations?
While this may sound obvious, It’s essential that someone in the organization actually jumps in and starts creating the internal formula for Total Landed Cost. It’s very easy to fall into the trap of believing that collecting reams of data will eventually result in the coalescence of that information into something useful. However, that’s more a type of magical thinking than anything else. So, start with what you’ve got: payment terms, transit time, manufacturing lead time, time to market and the costs to physically produce the product from a materials and labor standpoint. Then start adding in other potential costs such as:
- transportation
- warehousing
- delivery
- customs delays
- tariffs
- taxes
- import regulatory requirements
- documentation
- customs and border protection duties
Although it may seem daunting, getting a true sense of these costs is completely possible. Utilizing your company’s historical records in combination with information garnered from discussions with partners such as freight forwarders, importing companies and customs brokers should offer an excellent start in calculating the overall TLC for almost any product.