A machine shop can technically be any building, business, or specific shop floor area that is dedicated to CNC machining — a diverse group of subtractive fabrication and manufacturing processes. However, a true, end-to-end metal fabricator and machine shop is able to provide more than just simple machining operations and is home to many complex machining-related activities.
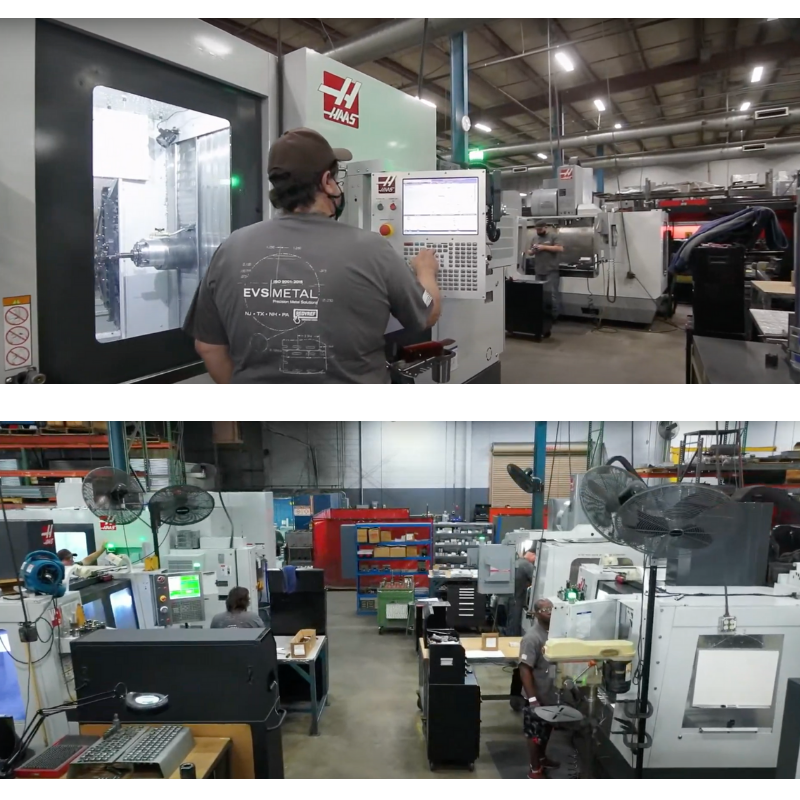
CNC Machining: The Core of Modern Machine Shops
Computer numerical controlled (CNC) machining is the foundation upon which modern machine shops build every other machining-related capability. The addition of CNC technology to machining equipment began in the late 1940s, but didn’t become commercially available until the 1970s. Prior to the 1980s, numerical-controlled (NC) systems were still considered the norm in machine shops. It wasn’t until 1989 that CNC machining became the industry standard for metal fabricators.
What Types of CNC Machining are Most Common in Machine Shops?
CNC mills and lathes are the two most common processes completed in most machine shops:
- Horizontal & Vertical CNC Machining Mills: Utilize rotating multipoint cutting tools to progressively remove metal or plastic material from a workpiece, resulting in a precision-machined end product. Face, plain, form and angular milling are all common CNC mill operations. Most mills are vertical, however, there are also some phenomenal horizontal mills available, like the Haas EC-400.
- CNC Machining Lathes: A CNC lathe is a machine that holds a part or material in place while rotating it via the main spindle. The lathe’s cutting tool removes metal as the piece rotates.
5 Reasons Why Machine Shops Utilize CNC Machining Technology
CNC technology is an important part of modern machine shops for a number of reasons:
- It’s the only way to ensure true precision for machined parts. Because CNC mills and lathes are computer-controlled, they can be programmed to carry out machining operations within much tighter tolerances than manual or NC workstations.
- CNC machining is more efficient, and therefore, more cost-effective for machine shops to run. Although CNC-enabled mills are a big investment, the returns on those investments are quick and substantial.
- They help eliminate human error, many of which can be extremely expensive to fix.
- CNC technology makes machine shops a safer place to work. Machinists do not come into contact with the machining tools; most are switched out automatically based on whatever program is currently running.
- CNC-enabled machining centers require less staff training to get up and running, as well as less setup time between jobs.
EVS Metal: Precision CNC Machine Shops in Pennsylvania & Texas
EVS Metal has four ISO 9001:2015-certified precision sheet metal fabrication facilities across the U.S. Our Stroudsburg, Pennsylvania and Pflugerville (Austin), Texas locations each house state-of-the-art machine shops with high-tech CNC machining centers. Some of the machines currently in use include:
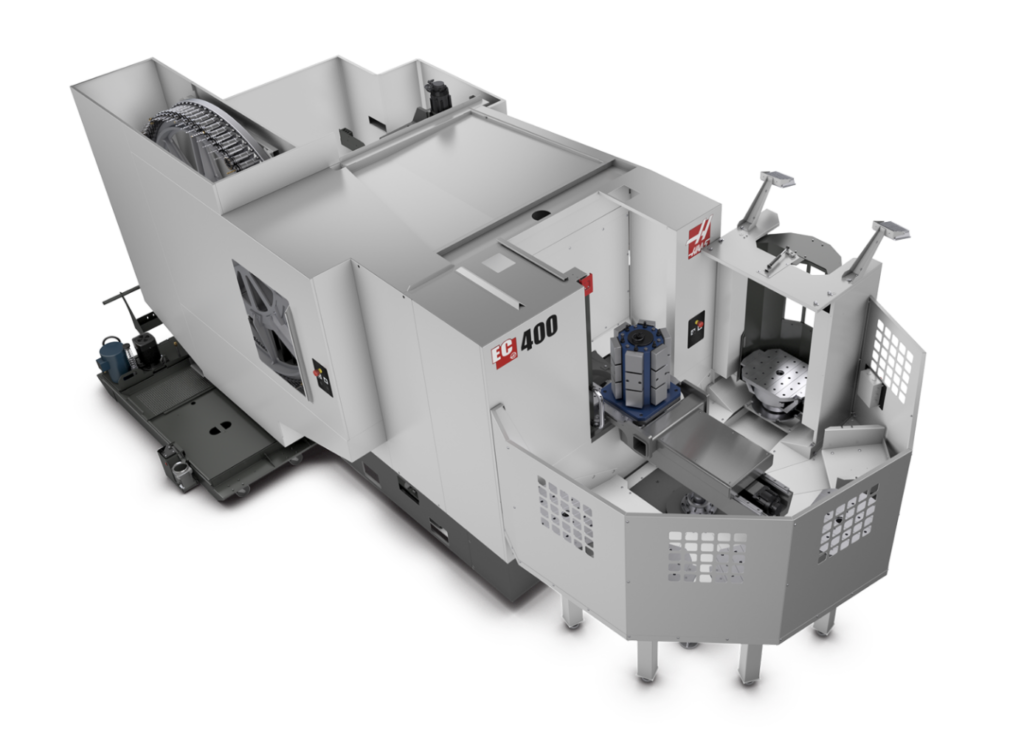
- Haas 2020 EC-400 Horizontal Machining Center
- Haas VF2 Vertical Machining Center
- Haas VF2-SS Vertical Machining Center
- Haas VF4 Vertical Machining Center
- Haas VF4SS Vertical Machining Center
- Haas ST-25Y CNC Turning Center
- Haas Servo Bar 300
As a result of the EVS’s investment in advanced machining technology, our company is able to perform secondary operations on aluminum, stainless steel, and plastic parts and products with incredible efficiency. This allows us to continuously serve our customers with the quality and efficiency they deserve.